MT HEPBURN COMPANY GOLD TREATMENT WORKS
SWIFTS CREEK-OMEO ROAD TONGIO, EAST GIPPSLAND SHIRE

-
Add to tour
You must log in to do that.
-
Share
-
Shortlist place
You must log in to do that.
- Download report
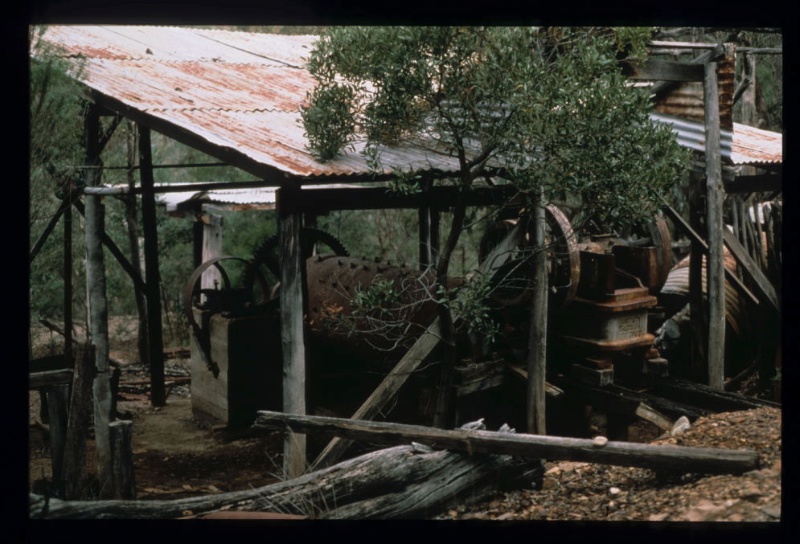
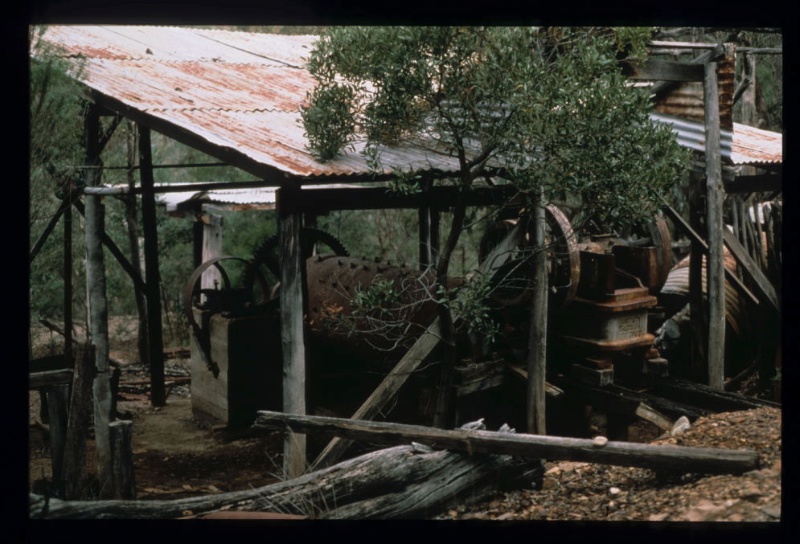
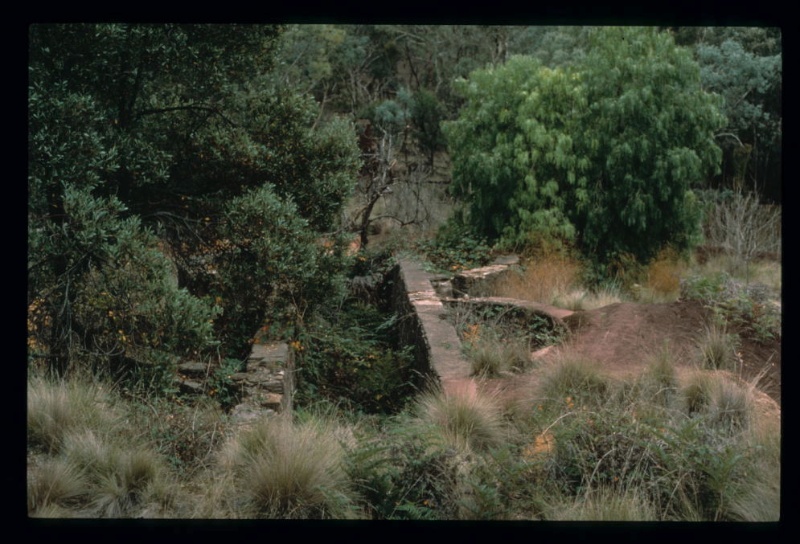
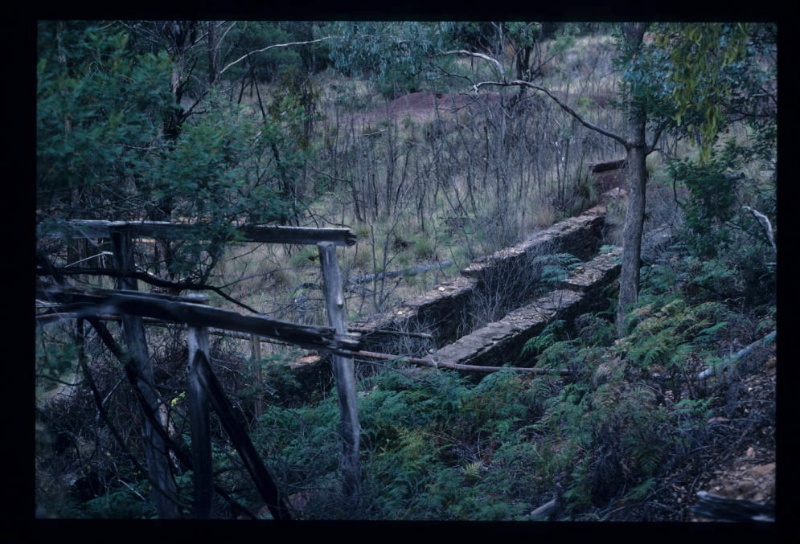

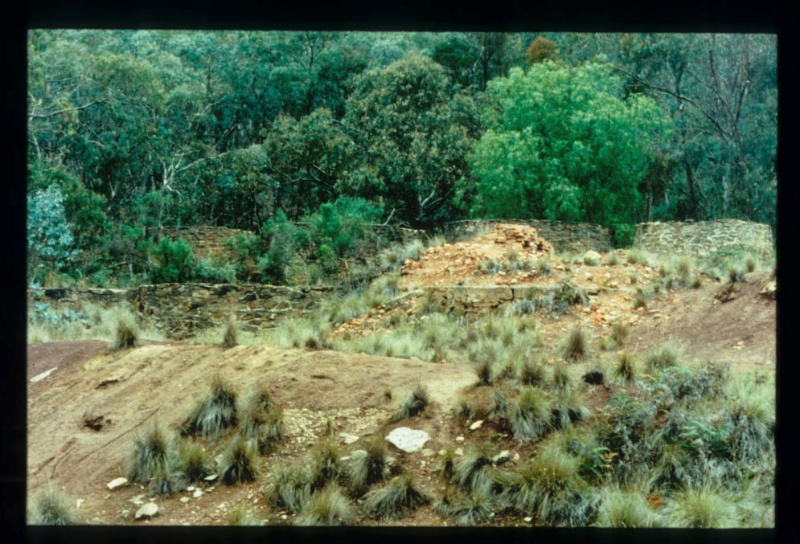
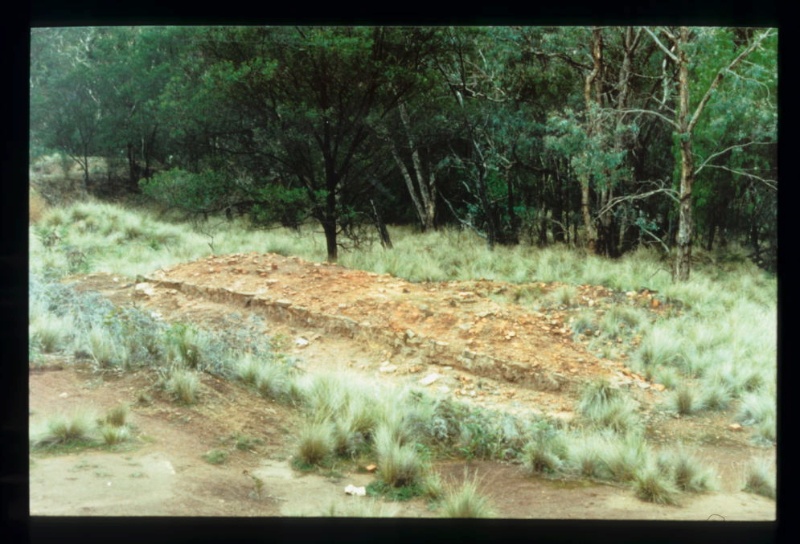
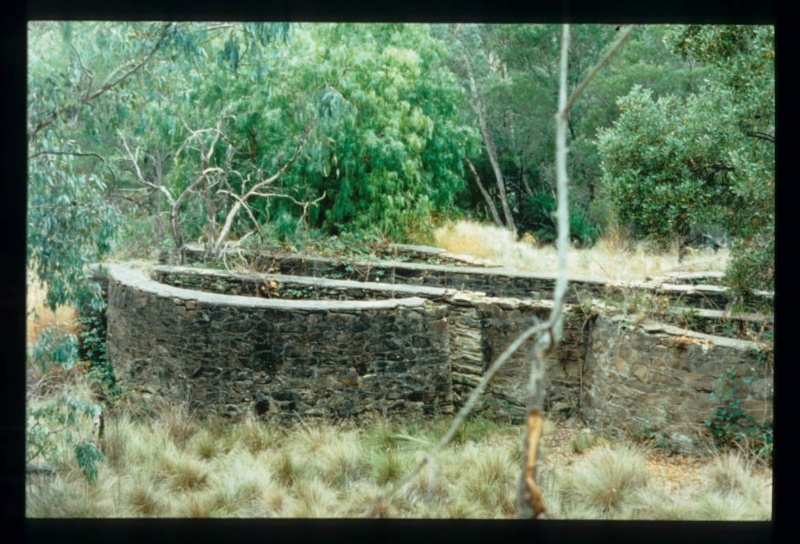
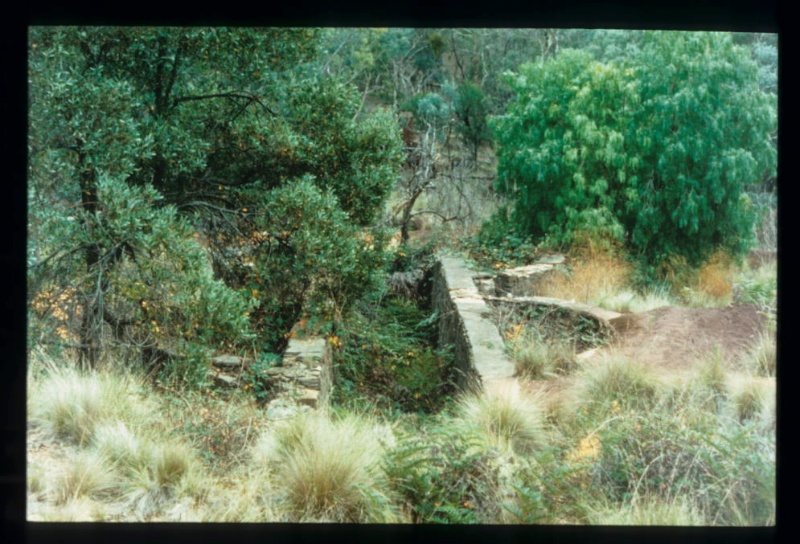
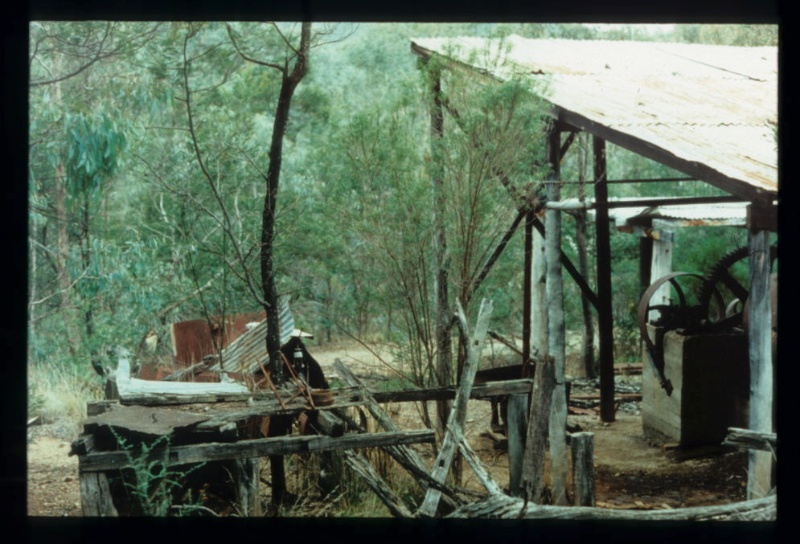
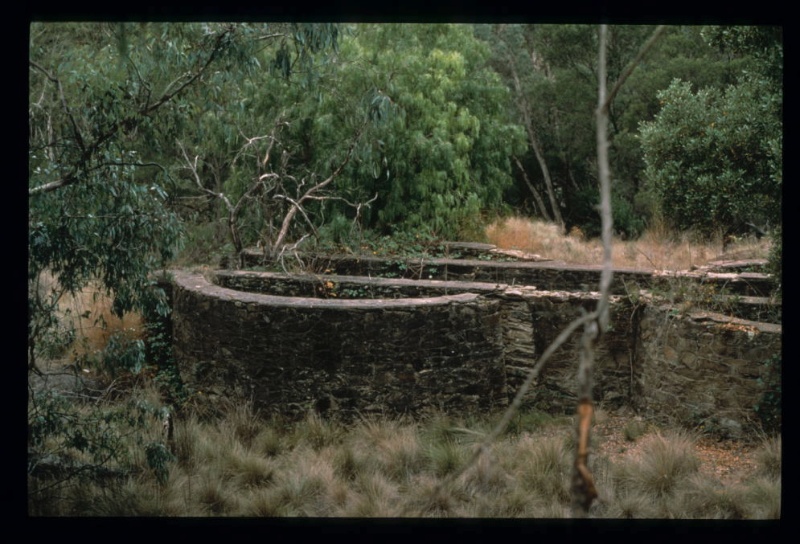
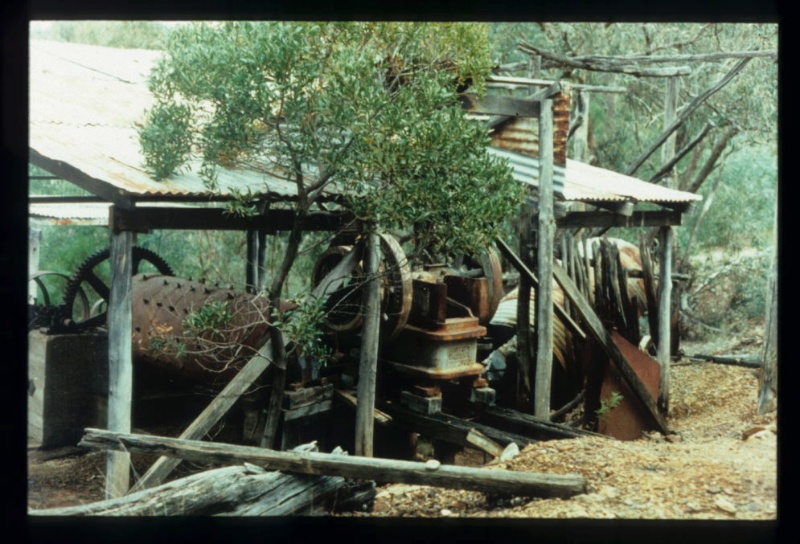
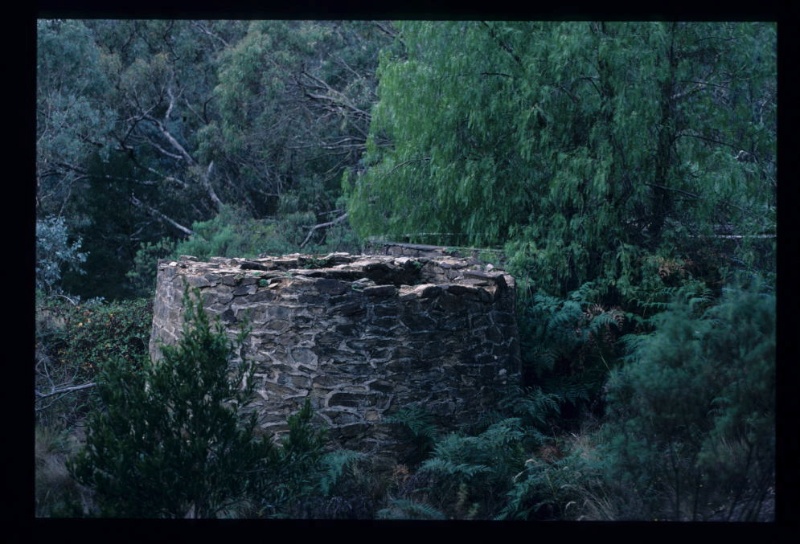
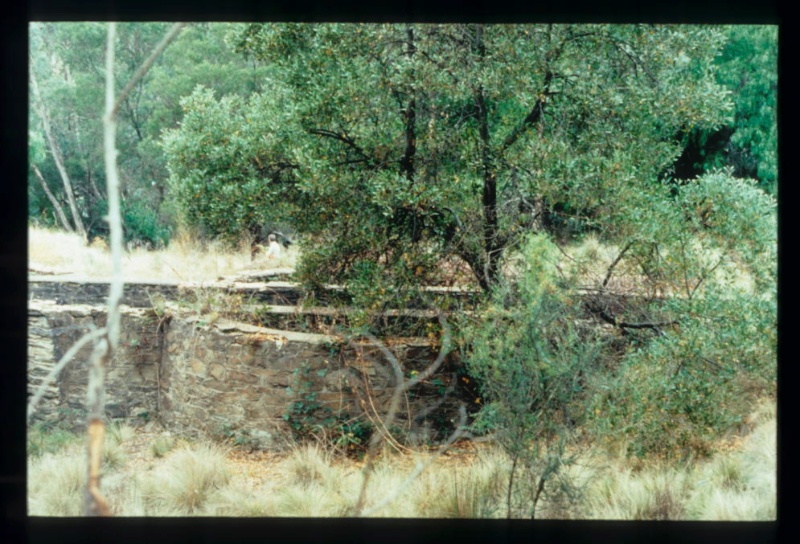
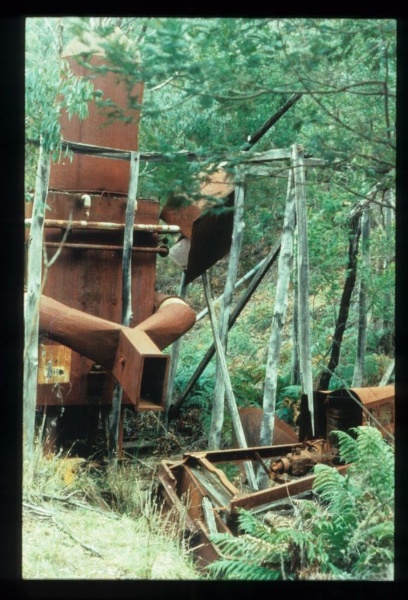
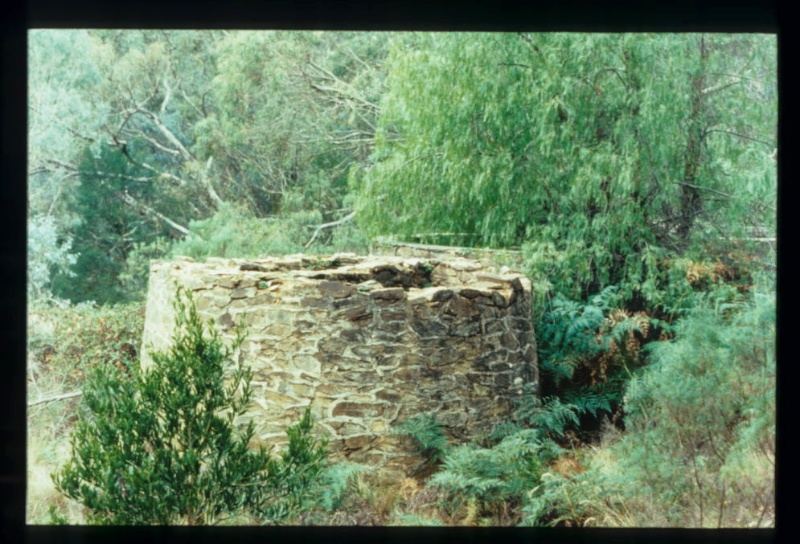
Statement of Significance
What is significant?
The Mount Hepburn Treatment Works is located near the junction of Power's Gully and Swifts Creek. It is the site of major mining operations from 1896 to 1907 and the elaborate plant and processes required to extract gold from refractory ore (heavily mineralised gold bearing rock). The mine was also briefly worked in the 1930s and 1940s. It is a complicated and extensive site with a series of adit levels, tramways and hut sites and a palimpsest of ore processing relics on the bank of Swifts Creek. The significant components include but are not limited to:
* stone piers – vat foundations and discharge tramway.
* Dumps of cyanided and calcined battery sands and pond.
* Bed of large reverberatory furnace, remnants of flue, stack base and other structures.
* Large ash dump containing ceramic and iron artefacts.
* Water-jacket blast furnace and small dump of slag.
* Clusters of scrap mining plant and vehicles.
* Barrel furnace, compressor, motor engine and associated material (slag and flint stones)
* Abandoned huts and sheds.
* In situ stone crusher, milling machinery and associated structures.
* Earthworks including lower-most mullock heap, tramway and cutting, water race and concrete reservoir.
How is it significant?
The Mount Hepburn Treatment Works is of historical and scientific significance to the State of Victoria.
Why is it significant?
The Mount Hepburn Treatment Works is historically important as a rare example of a once widespread type. In the 1870s Victorian miners began to have success in extracting gold from refractory ores through a process which involved roasting finely ground ore in reverberatory furnaces. In the late 1890s a new chemical process was added to the miner’s ore-retrieval repertoire which involved using solutions of cyanide. The cyanide process proved to be extremely important technology and is still the basis of gold recovery in the mining industry today. Example of both processes – roasting and cyaniding - occurs at the site and their importance at the time is clearly illustrated by the scale of the surviving heritage.
The Mount Hepburn Treatment Works is scientifically important for the survival of a range of relics documenting attempts to treat refractory ores through chemical and metallurgical means. Of crucial significance is the remains of the cyanide works, the surviving features ranging from very visible masonry structures to subtle traces. No other place in Victoria or possibly Australia can match the site, in extent, variety, archaeological or scientific potential in terms of surviving relics.
[Source: Victorian Heritage Register]
-
-
MT HEPBURN COMPANY GOLD TREATMENT WORKS - History
Heritage Inventory History of Site: In 1858, William Power made the first reef discovery in Gippsland near the junction of Power's Gully and Swifts Creek. His claim, named the Morning Light, formed part of the later Mt Hepburn–King Cassilis leases.The reefs in the vicinity of the later Mt Hepburn leases were first opened up in the late 1860s. A battery operated briefly, but was removed when the mines were abandoned in about 1870. The difficulty of retrieving gold from the complex, pyritic ore of the district was doubtless to blame for that early exodus.Mining entrepreneurs Ball and Smart took out leases on the Mt Hepburn ground in 1888, and initially crushed stone from their mine at their Brave George battery at Swift’s Creek. After the death of Smart in 1889, Ball continued the development of the mine. In 1893, his Mt Hepburn Co. installed an Otis ball mill (one of the first in Victoria) and short blanket tables, driven by 16-hp portable steam engine. The plant cost relatively little to run, but its lack of concentrating plant caused a substantial loss of gold in the tailings and operations were halted at the end of 1895. At that time, the Government Geologist, R.A.F. Murray, visited the mine and hailed it as the most remarkable on the field—at least, in terms of its potential yields. But he lamented that the company’s inadequate treatment plant allowed at least half the gold to escape with the tailings.In 1896, an English company, the Mt Hepburn Co. Ltd, was formed to take over the leases. The Otis mill was replaced by a traditional stamp battery made by Thompsons of Castlemaine. A 60-head battery was originally ordered, but was deemed excessive and only 20 heads were eventually delivered. A 90-horsepower boiler, intended to drive the 60-head battery, was also delivered but was never used. Also superfluous was a 60-ft high brick chimney stack, built on the hillside near the battery to serve the large boiler. Other works developed at this time included a water race from Upper Swifts Creek, water storage, and a new tramway from the Beehive level of the mine. In 1897, the Mt Hepburn Co. contracted with the General Exploration Co. (GEC) that the GEC could treat all its tailings. In return, the GEC agreed to build a cyanide treatment plant and pay the Mt Hepburn Co. a royalty on gold retrieved. In 1898, GEC constructed a large cyanide plant, costing £7,000 and said to be one of the best in Australia at that time.In September 1898, after just three months’ continuous crushing with their new battery, the Mt Hepburn Co. ceased operations, due to negligible gold returns. The stamp battery had achieved poorer returns than the old Otis mill: only 207 oz from 2,893 tons of ore. Summarising the performance of the Mt Hepburn Co. Ltd., Griffiths (1978) wrote that it ‘was floated on the premise of huge ore reserves and simple metallurgy, neither of which were investigated properly at the time, and both of which were quickly found to be incorrect.’ Shareholders lost some £180,000. The crushing plant was sold to the Cassilis GMC in 1900.The GEC’s cyaniding plant had commenced work in mid-1898. It was soon found that the plant’s operational capacity was only 720 tons per month, rather than the 3,000 tons anticipated. The complexities of the local ore resulted in low gold recovery, demanded a large consumption of lime, and lengthened the cyaniding process. Proving unprofitable, operations ceased in early 1900, and the cyanide plant was sold to the Allsop brothers (its former managers). At the same time, they acquired outbuildings, chimney stack, engine bases, and other structures from the defunct Mt Hepburn Co. The Allsops constructed an integrated treatment works on the Mt Hepburn site. Recognising the need to treat the pyritic Cassilis ores in a furnace prior to cyanidation, they installed a large desulphurising roasting furnace, complete with condensing chamber and 360ft-long ground flue connected to the unused 60-ft chimney. The furnace occupied the GEC’s former extraction house, between the southerly group of vat bases and the creek. It was one of the largest ore-roasting furnaces in Victoria, measuring 50 ft long and 10 ft high. In July 1901, J.L. Allsop, manager of the plant, died, aged just 34, as a result of inhaling the poisonous gases generated by the cyanide process.The Allsops’ plant treated tailings from local mines and from as far away as Sunnyside and Glen Wills. In fact, in 1901 most of the plant was moved to Sunnyside, to treat the huge volume of tailings on-site. Between 1900-03, it is estimated that the plant at Mt Hepburn treated 2,500 tons of concentrates and tailings for a yield of about 5,000 oz. The gold recovery process was said to have been nearly 95 per cent effective. In 1902, the King Cassilis GMC was formed. From 1904, the company rented Allsop’s treatment works, gradually modifying the plant to incorporate an economical Merton furnace, Dodge rock breaker, and a Niagara pulveriser (later replaced by a Krupp ball mill). The plant’s small size and unsuitability for the hard local ore resulted in poor yields, and the mine closed down in 1906. Since 1888, the Mt Hepburn/King Cassilis mine had yielded 1,852 oz from 4,172 tons of ore.In 1907, the remaining useful components of Allsop’s treatment works were removed to sites at Glen Wills and Sunnyside, and over the ensuing few years operations at Mt Hepburn were confined to the cyaniding of tailings remaining on the site. Some small-scale prospecting and mining took place prior to World War One. The King Cassilis leases were worked by the National Gold Mining and Milling Co. in the early 1930s. A small plant was installed, consisting of a 5-head battery with two concentrating tables, a small hand-charged reverberatory furnace, and cyanide plant. Only 220 tons of ore were treated, for a yield of 114 oz.J.D. Avery took up the leases in the late 1940s and erected a small water-jacketted blast furnace, in which he smelted ore for many years.Heritage Inventory Description
MT HEPBURN COMPANY GOLD TREATMENT WORKS - Heritage Inventory Description
Mine working and associated features - three adit levels including very large intact mullock heap, several stone fireplaces, concrete-lined dam and excavated powder magazine with stone-lined entrance. Also, treatment works consisting of three levels of vats and foundations largely buried.
Heritage Inventory Significance: National EstateScientific significanceùintactness, rarityùæThe Mt Hepburn/King Cassilis works provides us with the interesting relics and construction remainders associated with a great variety of ore reduction and treatment methods. It is doubtful if such a varied layout and assembly of basic remains related to complex ore treatment can be seen on any single site elsewhere in Victoria.Æ (Griffiths)
Heritage Inventory Site Features: MT HEPBURN TREATMENT WORKSVats and foundationsùThree levels of foundations which are largely buried by battery sand and partly obscured by vegetation.Upper levelùRow of four stone vats, each having one internal dividing wall. The vats are 13 ft in diameter, stand 9 ft high and have 2ft-thick walls.Middle levelù200 to 300m-long tramway cutting (6 ft wide) with 2ft-thick stone wall which cuts through six 23ft-diameter vat footings. The tramway runs through a brick archway under the one of the vats. This vat is sealed by a stone floor with the remains of a 12ft-square brick chimney stack base. The tramway cutting continues on from the vat foundations and terminates near AveryÆs iron blast furnace.Lower levelùAt least four 17ft-diameter vat foundations, largely buried by a large full slum pond. Also visible on the slum pond are the stone base of a roasting furnace (40 ft x 10 ft, most brickwork demolished) and another substantial structure with a floor and a row of three small vats. Near the furnace is another largely buried structure (stone footings) and a scatter of furnace ironwork.These remains represent treatment works operated on the site by a succession of companies: Mt Hepburn Co. Ltd (brick chimney stack, water raceù1896-1900); General Exploration Co. (cyanide vats and footings, tramwaysù1897-1900); Allsop brothers (1900-03); King Cassilis Co. (1904-6).The stone walls and piers for the General Exploration Co.Æs cyanide plant were constructed downhill from the Mt Hepburn battery in late 1897. The contractors brought skilled masons from Melbourne to build the walls of local schist. The vats themselves were made by Bowman and Bow, coopers of Maldon. Griffiths (p. 155) provides the following description of the GEC works, to which operation most of the structural remains relate.æTailings were taken by tramway from their discharge at the battery plates to six collecting vats, each of 60-ton capacity. Each collecting vat was built over a tramwayà After draining in the collecting vats the sands were discharged into trucks underneath which were hauled up an inclined tramway by means of a steam winch, to the top level of the six treatment vats, each of which was 23 foot diameter, 8 foot high and had a capacity of 90 tons. These also had a tramway underneath and after discharge of the sand again by bottom discharge doors, it was transferred by truck to the sand dump and dam.æPrior to discharge of the treated sand, the solution was run to four storage vats each 13 foot diameter, and thence through intermediate vats prior to its discharge into the electrolytic precipitation boxes which were 40 feet long and 6 feet 4 inches wide.æIn all there were 26 vats, the elevated vats being supported on circular walls or on semi-circular walls and the walls either side of the central discharge tramway.Æ AVERY'S MINING PLANTThe plant is surrounded by a extensive dump of modern processing equipment.Crushing shedùTimber-framed, galvanised iron roof. The shed contains a range of plant including a jaw crusher (manufactured by Jacques Bros. Pty Ltd, Richmond, Melbourne), rod mill, diesel engine, and generator.FurnaceùSmall iron blast furnace and slag dump. The blast furnace stands on the foundations of the earlier Mt Hepburn treatment works.AveryÆs plant was installed in the late 1940s and was used over a long period (until as recently as 1978?).
-
-
-
-
-
MOUNT HEPBURN COMPANY GOLD TREATMENT WORKSVictorian Heritage Register H1940
-
MT HEPBURN COMPANY GOLD TREATMENT WORKSVictorian Heritage Inventory
-
-